Jouni Kyllönen, SVP of sales at Mailroom Solutions, outlines how investing in the latest technologies has helped Posti Group Finland to strengthen its e-commerce parcel handling processes
When building a house, a strong and solid foundation is an essential part of the construction project. No matter how stylish the window frames or how beautiful the decorations, the most important thing is that the base is well built and can support the whole structure.
The same applies to postal systems – a strong base is required. Integrations are needed for various existing information systems, various sorting equipment must also be supported, and a lot of data for track and trace systems as well as statistics must be provided as well.
At Posti Group Finland, the Mailroom Manager back-end from Mailroom Solutions has been integrated with the existing information systems to enable OCR-based restmail sorting, which will then merge the machined and manual mailflow, registration of e-commerce parcels and later also barcode-based manual mail sorting.
The Mailroom Manager back-end allows the customer to select a suitable toolkit for various postal processes based on budget and required features. Posti Group wanted to be able to handle Far East e-commerce parcels conveniently with a single touch and automatically select the most cost-effective delivery methods. Mailroom Solutions was able to offer an OCR-based solution that combined up to five separate processes into a single process. “We expect this solution to bring us 50% cost savings in our e-commerce parcel process,” says Jukka Nevalainen, process manager at Posti Group Finland.
Posti Group has been working with printing house partners for years and most of the print products today contain a valid barcode that can be used for identifying the delivery address. Therefore, the post also needed a fast, manual solution for sorting barcoded oversized mailpieces based on sorting machine sort plans. In this case, the mSorter Code Mini was the ultimate solution; it is low cost, easy to integrate and requires just 10 minutes of operator training. With integration to the existing manual sorting furniture, Posti was also able to extend the lifespan of the existing hardware. Because it already had the Mailroom Manager back-end in production, the deployment of the barcode-based sorting solution was very straightforward.
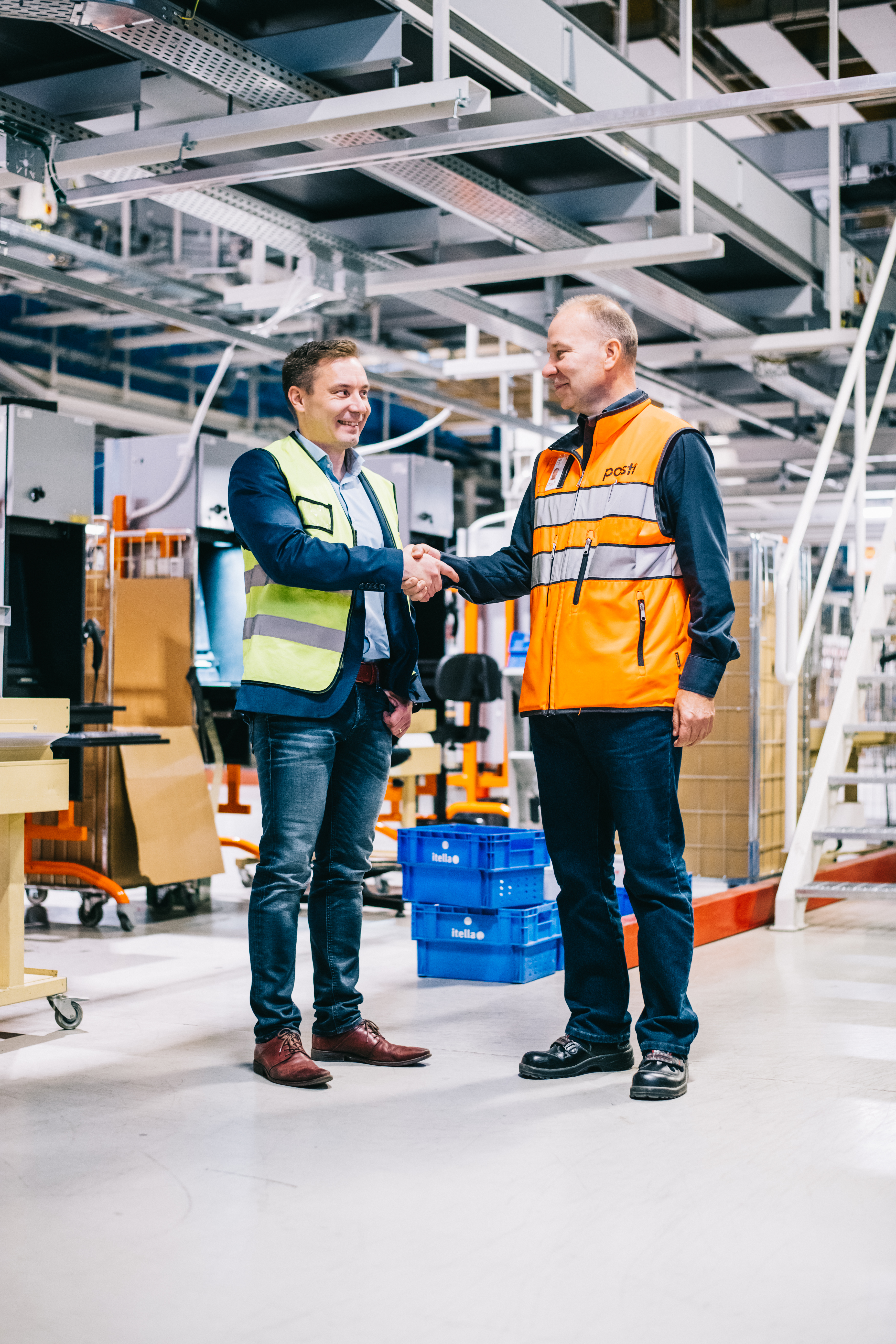
“Cooperation with the Mailroom Solutions team has been both smooth and convenient. We were surprised by their comprehensive knowledge of our business needs,” says Hannu Kolmonen, development manager at Posti Group Finland.
In addition to the main projects, dozens of smaller life-easing functionalities have been introduced with the help of a flexible and robust back end.
“The cooperation with Posti Group has taught us a lot about the importance of the open interfaces and the need for easy integration. We often need to merge data from several sources to make the enriched data available in the desired format,” says Janne Eteläaho, CEO of Mailroom Solutions.
While planning the renovation of the postal processes, it is essential to make sure that the selected back-end solution is able to support future needs as well. The solution must lay on open architecture and enable:
- Flexible interfaces and easy integration to upstream and downstream;
- Easy vertical and horizontal scalability;
- Wide range of sortation solutions to cover the whole business area.
In addition to this, observation of the process productivity is important. This makes it possible to proactively adjust the process and immediately correct possible bottlenecks. It is also essential for the floor level managers to access the statistics for every process during the work shift.

A postal process renovation is just like any other IT project. The more careful specification and sharp definition of requirements there is, the more likely the project is to succeed. Furthermore, the experts need to be involved in the early phase of the project to ensure its overall success.